Nikota Air Compressor Parts Manual
- Nikota Parts Replacement
- Nikota Parts
- Nikota 3500 Watt Generator Parts
- Nikota Air Compressor Parts Manual Pdf
Get great worksite performance with this portable twin tank air compressor. Dual tanks deliver more consistent line pressure and reduce the amount of moisture in the line, extending the life of your tools. Use this twin tank compressor on rooftops, jobsites or the garage. Air delivery: 3.5 CFM @. Nikota Twin Tank Air Compressor, 2-HP, 4-Gal, 115V is available on HiBid. View this auction and search for other auctions now on the leading online auction platform.
Here are a few guidelines on how to keep your air compressor working optimally. Even if you own a cheap air compressor, keeping it lubricated, free of water accumulation and with proper air filtering you’ll be able to extend it’s working life and obtain a trustworthy tool for years to come.
Oil, Lubrication
Your air compressor is basically an engine, and as such it requires constant lubrication to prevent excessive friction from damaging the moving parts and ultimately seizing the piston/s.
Regularly check the oil level, some compressors will have a dipstick on the oil cap, others will have an oil level gauge like this one:
The oil gauge on an inexpensive air compressor showing the level is OK.
These are just as easy to read, the red dot represents the “OK” mark (I don’t know why they paint it red, should’ve been green) – Ideally you want to keep the oil level within the center of the dot, but as long as the level is within the dot, you are OK.
On these it’s also easier to judge the state of the oil by looking at it with a flashlight, you can often see whether it’s getting milky (water) or darker (regular wear) without having to remove a sample from the crankcase.
Oil is regularly lost through the exhaust and the breather hole on the crankcase. Oil also ages and because of this, you should replace the oil after a certain amount of duty hours. The actual time depends on many factors and it’s best if you obtain the manual for your particular compressor for a clear indication on when to replace the oil.
Non detergent lubricants are preferred, make sure you respect the viscosity the manufacturer suggests for your particular compressor.
It’s also important not to overfill them with oil as you can cause several issues, if the oil level is too high the oil can get whipped and it will foam up, losing some of it’s properties but most importantly it will gain volume, further increasing your problems.
So keep checking with your dipstick/gauge as you refill with oil and make sure your unit is perfectly level to the ground when you do this.
To remove the old oil there’s going to be a bolt at the bottom side or the bottom of the crankcase in all air compressors, all you need is a wrench. Make sure you remove the oil when it’s warm and to speed up the process even further, also remove the filling cap so you don’t draw a vacuum.
Purging
As the compressor’s intake happens to be our breathable atmosphere, humidity in the air is sucked in on every cycle. It doesn’t help that the compressor head heats up during it’s this compression cycle. As water will condensate and accumulate in the tank/s, it’s imperative to purge the tank/s at least once a week.
A common type of release valve found on most small to medium sized compressors.
Purging is easy, locate the release valve at the bottom of the tank and open it, once relatively little water comes out, close it. You don’t have to empty the tank/s every time you purge, but it is recommended you do so if you plan to store the compressor for a long period of time. If you feel the purge valve doesn’t seem to open all the way, close it and open it again; there could be some sludge blocking it.
For extended periods of storage, drain the entire tank and remove the purge valve entirely, leave it open so the water can drip and dry on it’s own. Make sure to place the purge valve cap in a secured location so you don’t lose it!
If you don’t purge, the water will rust the tank’s envelope and ultimately a puncture will occur. The tanks are naturally coated with oil from the compressor, but it can’t always protect the steel from rusting. The more that water sits in there, the worse it’ll get in time.
To automate this task there are several solutions on the market, but some are rather expensive. These are basically solenoid valves with a timer, some work by venting after a compression cycle (that is, when the tank is filled up, a bit of pressure is released to remove the accumulated water). These solutions are often implemented in big compressor setups. More commonly are timed interval purge valves that will open once a designated period of time, usually you set them to once a week.
Nikota Parts Replacement
If you were to roll your own, the hardest part would be finding a solenoid valve that is rated for your maximum operating pressure and that also couples to the existing fitting on the tank. The circuit would be a simple timer. I would personally implement it using a micro-controller so I can have the long timer (let’s say 1-7 days) and then a one-shot output for the relay that would ultimately drive the solenoid valve. By using a uC you are open to many possibilities such as a warning alarm before the purge cycle to alert anyone around the tank.
Air filtering
The quality of the air entering the compressor is important, for one to protect the compressor head but also to reduce impurities in the air source, if you are going to be spray painting then you’d already have a filtering system in place, but reducing the amount of pollutants will help extend the life of those filters. It’s also worth mentioning that some air filters will have a silencer built in, to reduce the noise of your compressor; so that’s worth checking out!
If you are going to stick with the original foam filter on your cheap air compressor, you can spray a bit of filter oil to improve it’s performance, the way you apply it is by spraying some on the foam and then squeezing the foam so it penetrates throughout. You only need enough so the dust will stick to the oil and become suspended on the foam, you don’t want to use enough oil that it drips because this will clog the foam and also introduce excessive oil into the air stream.
A cheap alternative to the plastic foam filters is an automotive oil filter, these can work with plain air just fine and they have a very convenient thread size, all you need is a male adapter since both ends would be female. You could check out the air filters for scooters and small motorcycles, but they may not have the same thread size. You definitely don’t want to use a smaller thread size as this will constrict the intake flow and increase the noise as well.
With these simple guidelines your air compressor will run properly for a very long time, take -your- time and follow them thoroughly!
Cheers.
Save money and troubles by learning how to set your air compressor pressure switch the right way!
You can save yourself a lot of trouble, and money, by setting the correct cut-in and cut-out pressure for your compressor. Learn how to set the pressure switch yourself!
First I will teach you what the correct pressure settings are for your compressor. Than I will show you how to set these pressures on your pressure switch.
The right pressure
Both for small (piston) compressors and for large industrial rotary screw compressors, the pressure setting is the most basic and most important setting of the compressor.
On smaller compressor, the pressure is set up on the pressure switch. On large compressors, it’s done on the central compressor controller, but the idea is the same.
Less is more
When deciding what the best pressure is for you and your compressor, always remember to set the pressure as low as possible for your application.
I know most compressor are advertised as 7 bar (125 psi) compressor, and are set at the pressure when you buy them. But if you only need 5 or 6 bar, it’s better to lower the pressure.
Every increase in pressure will require more energy. Simple as that. If you own a large compressor ( say 30 kW or bigger), you can save hundreds or thousands of dollars per year in energy costs by lowering the pressure setpoint.
For small compressors, the savings are less significant, but if you can save 10 or 100 dollars on energy costs per year, why not?
Cut-in and cut-out pressure
A compressors always has two pressure set-points: the cut-in and the cut-out setpoint.
These are simply the two pressures at which the compressor starts and stops. The compressor will stop when it reaches the cut-out pressure and will start again when the pressure drops back to the cut-in pressure.
So, the cut-in pressure is always lower than the cut-out pressure. We call the difference between cut-in and cut-out pressure the pressure band or the pressure differential.
A rule of thumb is that the pressure differential of at least 1 bar (14 psi).
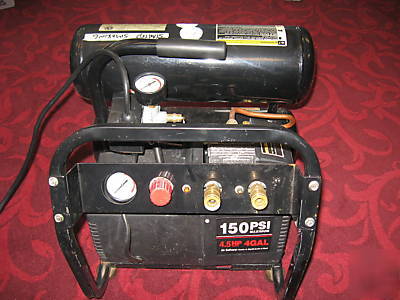
If the difference between the cut-in pressure and the cut-out pressure is set too small, the compressor will quickly start and stop repeatedly.
This will burn the compressor motor, will cause extra wear on the compressor components and will damage the pressure switch.
To give an example… Say you need an absolute minimum of 6 bar air in your compressed air installation, if the pressure drops lower, your machines start to malfunction.
You set the minimum pressure on the pressure switch at 6 bar (or 6.1 to be sure) and you set the maximum pressure at 7.1 bar.
Now you always have an high enough pressure in your compressed air system, and you made sure that the compressor stays healthy by not having it start and stop all the time.
Cut-in pressure is 6.1 bar. Pressure differential is 1 bar. This makes the cut-out pressure 7.1 bar.
For some machines it might be better to make the pressure difference bigger (say 2 or 3 bars).
This is better for machines that only run for a very short time.
When you increase the pressure band, the compressor will run longer and has more time to heat up to remove any water or moisture inside the compressor (the number one enemy of compressors!).
Setting the pressure switch
Depending on the make and model of pressure switch, one can adjust only the pressure setting, with a fixed differential, or one can adjust both the pressure setting and the differential.
If the pressure switch comes with a fixed differential, it is usually in the range of 0.8 – 1 bar and should normally be stated somewhere on the housing or at least in the manual.
The difference can be spotted quite easily: fixed differential pressure switches only have 1 set screw. Pressure switches with an adjustable differential have a smaller second set-screw.
Setting the pressure switch seems straightforward enough. Just set the cut-in and cut-out pressures, right. Well, from personal experience I can say that it can sometimes be quite frustrating.. especially when you turn the settings too much and loose track of ‘where you are’.
I always tend to think think that the pressure switch sets the upper pressure limit with the main adjust screw. That is, I think, what makes it sometimes so frustrating to setup such a ‘simple’ device…
On most (but not all…) pressure switches, the big set-screw is to set the cut-in pressure. In other words.. to set the lowest pressure. The pressure where the compressor starts-up. Thinking about it, this makes sense, as this is the most important thing for your machine to operate properly (they will operate properly on a higher pressure, but not on a lower pressure).
The smaller screw, the differential setting, then sets the maximum pressure, the cut-out pressure, relative to the cut-in pressure.
So when you change the cut-in pressure (big screw), the cut-out pressure will also change, as it depends on and is on a fixed value away from, the cut-in pressure.
That’s what makes it sometimes so frustrating to set the pressure correctly.
Example of set-screws for cut-in and differential pressure.
(This is a Condor MDR 11/11 pressure switch, which are very common)
Step-by-step procedure:
Since the cut-out pressure is defined as the cut-in pressure + the pressure differential, it’s best to first set the cut-in pressure.
Nikota Parts
Setting the cut-in pressure.
- Starting from an empty tank. Start the compressor and let it run until it reaches the cut-out pressure.
- Open a drain to slowly let some air escape. Watch how the pressure slowly comes down.
- Wait until the compressor starts. Write down the pressure. This is the cut-in pressure.
- Adjust the cut-in pressure with the big set screw. Turn clockwise to increase the cut-in pressure.
- Close the drain valve. The compressor will run until the cut-out pressure is reached.
Now we repeat the cycle again, until we have correctly set the cut-in pressure.
- Open a drain valve to slowly let the compressed air escape and wait until the compressor starts.
- Note the pressure at which it starts (the cut-in pressure). Adjust when necessary.
After a few cycles you should have successfully set the cut-in pressure. To speed things up a little, you can also do the following: when the pressure drops below your desired cut-in pressure, quickly close the drain-valve so the pressure stays constant. Now adjust the set-screw (the big one), clock-wise (increase cut-in pressure) until the compressor starts. Depending on how far the actual pressure is below your desired cut-in pressure, turn the screw a little further (quarter-turn or less). Now the cut-in pressure should already be more-or-less OK.
Setting the cut-out pressure
The procedure is somewhat the same as for the cut-in pressure. Now only touch the set-screw for the differential pressure. If you don’t have this set-screw, you have a pressure switch with fixed differential, and you are done now 🙂
- Note the pressure at which the machine stopped last time you let it run.
- Adjust the differential pressure accordingly. Turn clockwise to increase (if you want a higher maximum pressure) or count-clockwise to decrease (if you want a lower maximum pressure.
- Open the drain valve and wait until the pressure drops low enough to start the compressor. Close the drain valve.
- Wait for the compressor to stop. Check the cut-out pressure.
- Repeat.
Reminder
Set the cut-in pressure first. Set the cut-out pressure second.
You have now successfully set the pressure switch.
Nikota 3500 Watt Generator Parts
The procedure can be different depending on your air
compressor pressure switch type. Some pressure switches can only be adjusted when under pressure. Don’t turn any of the screws when there is zero pressure in the tank, or when your just get your new pressure switch out of the box. Always check the manual, just to be sure.
Nikota Air Compressor Parts Manual Pdf
Most pressure switches are factory-set at a cut-in pressure of 6 bar with a pressure differential of 1 bar (which makes the cut-out pressure 7 bar).
I have made a basic overview of different models and types of pressure switches. Check out that page if you’re interested. And when you’re looking to buy a pressure switch, check out my buying a pressure switch page.